バット作り、匠の技に迫る
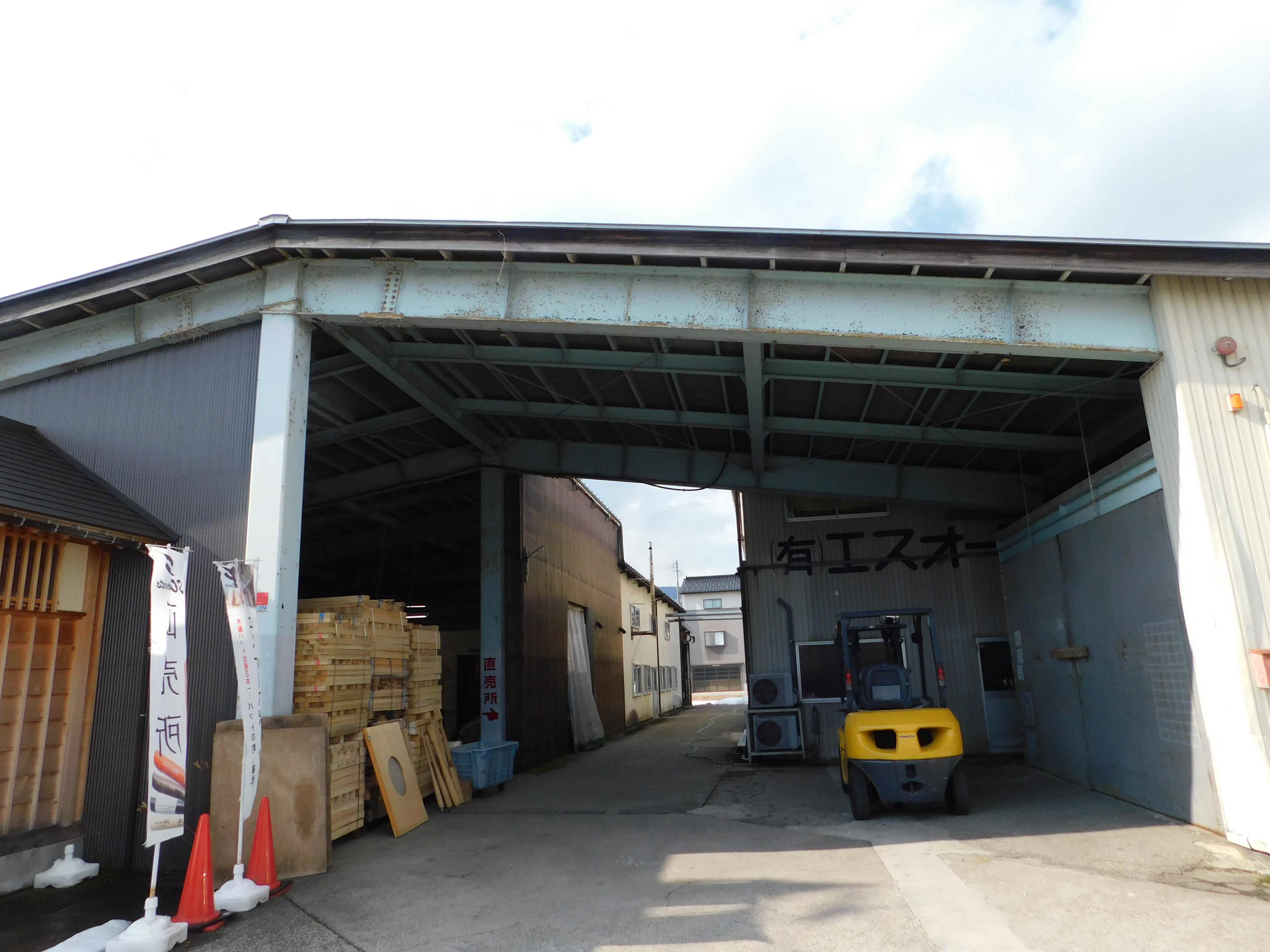
バット作り、匠の技に迫る
バットとグラブは野球用具の代表格です。バットの国内最大の産地としては富山県南砺市の福光地区が知られています。南砺市は富山県南西部に広がる砺波平野に位置し、石川県との県境に接しています。その南砺市福光にあるバットメーカーの一つ、有限会社エスオースポーツ工業にてバット作りについて教えてもらいました。
日本一のバットの産地、南砺市へ
バットが数多く生産されているという南砺市を筆者が訪れたのは1月下旬の穏やかな晴れの日でした。高岡駅からJR城端線のディーゼル列車に揺られること約40分で福光駅に到着。近くには南砺バットミュージアムもあり、「バットの産地」であることが分かります。
>>https://nantobat.jimdofree.com/
駅から徒歩で約20分、バット工場のあるエスオースポーツ工業に着きました。工場内を案内してくれたのは、同社代表の中塚陸歩さんです。
工場の入り口付近には、バットの原材料となる角材が丁寧に積み上げられています。ここに置かれているのは北海道などから入ってきた材料です。バットの原料にはアオダモ、ヤチダモなど何種類もありますが、ここにあるのはメイブルです。業者から入ってくる原材料は、このような角材の形で入ってくるとのこと。
さて、バットが出来上がるまでの工程には、大きく分けて乾燥、削り、塗装といった作業があり、最後に検品、包装されたのち販売されることになります。削りにはまず粗削りという丸棒にするという作業もあり、塗装の際にはマークも入れられます。
バット作りの基本、「木を知ること」
入ってきた材料(角材)はいきなり削るのではなく乾燥させるのですが、これは木材が水分を含んでいるためです。樹木は大地から水分を得て日光を浴びながら上へ伸びて大きくなる植物、当然といえば当然です。
また、この最初の段階で材料(角材)の状態を見極める必要があります。木目の状態、節の有無、重さなどなど角材をどのように使えばいいのかを判断する必要があるのです。ここにある角材は全て同じサイズですが、木目や節の有無、場所は異なり、それぞれ重さも違います。したがって、同じ重さのバットを作れる本数は限られてきます。例えば、材料を無駄なく使うことを考えながら角材のどちら側をグリップにすればよいのか、硬式用のバットとして重すぎるのか軽すぎるのかなどなど中塚さんの説明を聞くだけで、バット作りは非常に奥が深く技術が必要、材料を見る眼も必要な仕事だと筆者は感じました。木材の特性を知り尽くすこともバット職人にとっては欠かせない能力の一つなのです。
一本の樹木がバット用に使われるまでに、まっすぐに伸びるよう枝を伐採しながら育てられますが、大きく育つまでに40~50年かかります。しかし、樹木の上の方はバットに適さないため、一本の樹木から多くても20本程度のバットしか作ることができません。バットに適した森林資源を枯渇させないための取り組みをしている団体もありますが、もっと広がってほしいと筆者は思います。
>>https://www.aodamo.net/index.php
「手削り」でオーダーメイドに対応
バット作りには、材料(角材)の仕入れや管理から仕上げまでどの工程が欠けてもいいものは出来上がりません。この中で筆者が最も関心があったのが削りと呼ばれる工程です。一本の木がどのようにしてバットの形になるのかという過程が知りたいという興味がありました。
その前に、エスオースポーツ工業ではかつて大手メーカーの製品を作っていたものの、現在ではオリジナルブランドを立ち上げ、自社製品を作るという体制になっています。基本的には機械を使い自動でバットを削っていき、大量生産も可能です。が、オーダーメイドにも対応し、個々の注文に合わせて手削りもしているとのことです。機械削りのバットと手削りのバットを合わせて、年間1万本くらい製造しています。
南砺市ではかつて11社あったバットメーカーも現在は同社も含め合計5社のみ。この中で手削りを残しオーダーメイドに対応しているのがエスオースポーツ工業だけです。オーダーメイドのバットは使い手(選手)の具体的な要望に応じるため、同社にとって強みといえる部分になっています。それだけ作る各職人の技術力と感性、そして経験が必要になってくるのです。そんな中、同社には中塚さんを含め4人の職人が働いています。以前は8人いたものの、現在は4人に減った分、どの工程も全てこなしていると中塚さんはいいます。
「手削り」は職人技
ここで実際に粗削りされた丸棒を削りバットの形に仕上げる作業を見せてもらいました。
まずは機械を使い自動で削っていくところです。丸棒を固定し、機械が動き出すと10分もすれば綺麗なバットの形に仕上がっていました。データを入力するだけで指定した寸法のバットが仕上がるために大量生産に向いていますが、細やかな感触などが求められるオーダーメイドのバットには手削りでないと対応できないのです。
次に、手削りを中塚さんが実際に「実演」してくれました。
手削りに使用する機械を念入りに調整する中塚さんの姿はベテランの職人そのもの。そして、削りの作業の入ると先端部からバットの形にしていき、グリップ部分を中心に皮を剥ぐように丁寧に仕上げていきます。横で見ている私には、丸棒をいとも簡単にバットに仕上げたように見えましたが、中塚さんによると「簡単そうに見えて実際には難しい。腕のいい職人ほど簡単そうにやってみせる」と教えてくれました。実際にオーダーメイドに対応するには、見本のバットを参考にしながら削っていくそうです。手削りがこなせるようになるまでは、人にはよるものの3年くらいはかかると中塚さん。
最後に仕上げの工程があり、この段階で研磨や塗装もされていきます。そして、「商品」として日の目を見ることになるのです。
オーダーメイドだけでなく直売所も充実!
同社では敷地内に直売所があり、カラフルな色彩に仕上げられたバットがたくさん並べられています。これらを手に取り、比較しながら自分に合ったバットを購入できるようになっています。
現在では、大抵のモノはインターネットで欲しいモノを探し即購入できるようになりました。しかし、中塚さんは、「できればバットは実際に手に取って選んでもらえれば」といいます。バットの手触り、感触、重さや長さといったものは手にしてみないと伝わってきませんし、筆者自身、今回、バットを手に取って実際に触れたことで木の温かみを感じとることができました。
また、エスオースポーツ工業では工場見学も受け入れています。どのような過程を経てバットが出来上がっていくのか、熟練の技を見てもらいたいと筆者は思います。
木製バット業界の現状と未来は?
今回の取材に際して、筆者は木製のバットが年間にどの程度作られているのかを調べてみました。が、木製バットに関する公的な統計はなく、業界としても具体的な数値は把握していないようです。
ただ、アマチュアで金属バットが導入されたことで昭和50年代に年間100万本を切り、平成期には50万本を下回っている(うち、1992年の南砺市では全国の半分程度の15万本弱)と推測されますが、今後は少子化や野球人口の減少も懸念されます。
これだけみればバット業界の将来が心配になりますが、海外では大谷翔平選手ら日本人選手がMLBで多数活躍しています。今後、野球人気の復権で野球人口が増加することで、バット業界にも明るい未来が来ることが期待されます。
参考文献
『福光バット製造業産地診断報告書』富山県商工労働部経営指導課 1991年
『ビジュアル富山百科』富山新聞社 1994年
脇田健史、松下幸司共著「野球用木製バットの材種と流通」『森林応用研究』第24巻2号 2015年